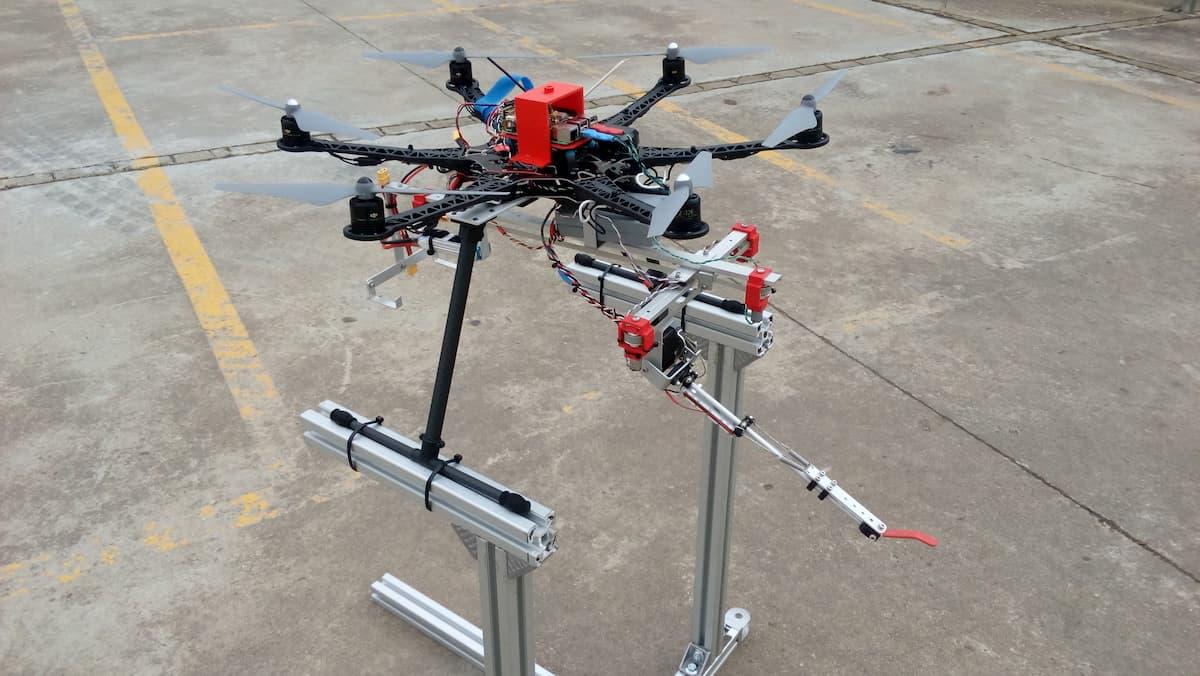
Ein fliegender Roboter
Hardwarepreis:
Konstruktion
DIY
Gewicht
leicht
Bildungsprojekt
Luftmanipulationsroboter: Kombination von Drohnen und robotischer Präzision für industrielle Anwendungen
Studierende der Universität Sevilla haben einen innovativen Luftmanipulationsroboter entwickelt, der eine Drohne mit einem Roboterarm kombiniert, um die Fähigkeiten traditioneller Drohnen zu erweitern. Dieses System ermöglicht Aufgaben über die visuelle Inspektion hinaus und erreicht abgelegene oder hochgelegene Bereiche für Inspektionen und Wartung in Branchen wie Öl- und Gasraffinerien, Stromleitungen, Solarparks und Chemiefabriken. Der kartesische Manipulator, der mit igus® Linearführungssystemen gebaut wurde, gewährleistet kontrollierte physische Interaktionen mit der Umgebung und bietet durch nachgiebige Gelenkmechanismen Stabilität und Sicherheit bei Zusammenstößen oder Überlastungen.
Was ist die Anwendung?
Der Luftmanipulationsroboter automatisiert Inspektions-, Greif-, Wartungsaufgaben und Umgebungsinteraktionen, ideal für Szenarien, die präzise und dennoch leichte Werkzeuge an schwierigen Höhen erfordern.
Was sind die Vorteile der Lösung?
Erweiterte Reichweite: Arbeitet in abgelegenen und hoch gelegenen Bereichen.
Kosteneffizientes Design: Leichte Konstruktion reduziert die Gesamtkosten.
Sicherheitsmerkmale: Nachgiebige Mechanismen schützen vor Überlastungen und Zusammenstößen.
Was sind die Vorteile des Roboters?
Die Drohne mit Manipulator bietet:
Hohe Präzision: Exakte Messung von Verformungen in elastischen Komponenten.
Resilienz: Stabilität und Langlebigkeit unter anspruchsvollen Umweltbedingungen.
Fortschrittliche Komponenten: Verwendung von igus® Linearführungen für sanfte Bewegungen und Zuverlässigkeit.
Industrielle Wartung durch Luftmanipulatoren transformieren
Dieser Luftmanipulationsroboter zeigt, wie Drohnen mit Roboterarmen industrielle Arbeitsabläufe revolutionieren können. Mit präzisem Handling, sicherheitskonformen Mechanismen und kosteneffizienten Designs bietet er eine innovative Lösung für Branchen, die eine effiziente, entfernte und zuverlässige Automatisierung bei Inspektions- und Wartungsaufgaben suchen.
1 Komponente