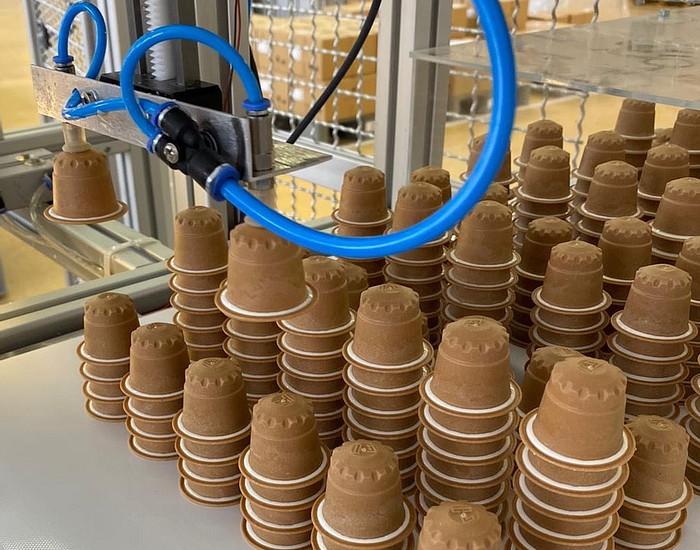
Automatisches Handling von Kaffee-Kapseln
Hardwarepreis:
Aufbauzeit
8
Stunden
Pick-Rate
30
pro Minute
ROI
1
Monat
Automatisierte Herstellung von Kaffeekapseln mit igus Portal:
Präzision und Nachhaltigkeit
Die rezemo GmbH entwickelt innovative Verpackungslösungen, darunter Kaffeekapseln aus Holz, die zu 100 % erneuerbar und frei von Mikroplastik sind. Eine zentrale Herausforderung besteht darin, sicherzustellen, dass die Kapseln mit Naturkautschuk korrekt versiegelt werden, um hohem Wasserdruck während der Kaffeezubereitung standzuhalten. Um Effizienz und Skalierbarkeit zu verbessern, setzt rezemo auf Low-Cost-Automatisierung mit einem igus 2-Achs-Portal und einem dryve D1-Controller, nahtlos integriert in ein Python-basiertes Steuerungssystem auf einem Raspberry Pi.
Was ist die Anwendung?
Das automatisierte System übernimmt die Verarbeitung der Kapseln nach der Befüllung, indem es sie mit einem Vakuumgreifer entfernt, auf einem zeitlich gesteuerten Förderband stapelt und in einen Trocknungstunnel zur Endbearbeitung transportiert.
Welche Vorteile bietet die Lösung?
Schmierfreier Betrieb: Gewährleistet kontaminationsfreie Handhabung von lebensmittelgeeigneten Produkten.
Kosteneffizienz: Eine erschwingliche Investition, ideal für Start-ups.
Hohe Haltbarkeit: Arbeitet zuverlässig über Millionen von Zyklen hinweg.
Welche Vorteile bietet der Roboter?
Das igus Lineportal bietet entscheidende Vorteile für die Verpackungsautomatisierung:
Präzise Bewegungen: Hohe Wiederholgenauigkeit für konsistente Stapelaufgaben.
Einfache Integration: Lässt sich nahtlos in Raspberry-Pi-gesteuerte Systeme einfügen.
Skalierbarkeit: Ermöglicht schrittweise Erweiterung der Produktionskapazität.
Fortschrittliche nachhaltige Verpackung durch Low-Cost-Automatisierung
Der Einsatz von igus Portalen bei rezemo verwandelt die Produktion von Kaffeekapseln in eine effiziente und skalierbare Operation. Durch die saubere Handhabung, Kostensenkungen und Unterstützung von erneuerbaren Materialien erfüllt das System nachhaltige Ziele und steigert gleichzeitig die Produktivität – ein beeindruckendes Beispiel dafür, wie Automatisierung einen echten Beitrag zur umweltfreundlichen Fertigung leisten kann.
3 Komponenten